Von Jens Fischer
Es zischt und funkt, wenn der Laserstrahl wie ein Zauberstab seine Runden durch den Metallsand dreht und dessen drei Hundertstel Millimeter kleinen Körnchen genau dort schmilzt und miteinander verschweißt, wo er sie berührt. Beim Erkalten bleibt eine gehärtete Schicht zurück. Der Vorgang wiederholt sich so lange, bis sich ein zuvor im Computer designtes Objekt aus dem metallisch grauen Staubbett erhebt.
Dieses dreidimensionale Schweißen, 3-D-Druck genannt, ist keine Magie, sondern von Menschen gemachte Hightech, die gerade rasante Entwicklungsschritte vollzieht. Daher will Airbus zukünftig zehn Prozent seiner Flugzeug- und Raketenbauteile nicht mehr von externen Dienstleistern kaufen, einlagern und im Bedarfsfalle weltweit zu den Flughafen-Werkstätten transportieren, wo sie verbaut werden, sondern von einem Ersatzteildrucker vor Ort produzieren lassen. Derzeit müssen alle Teile noch aus Blöcken des Werkstoffs gefräst, gedreht, gebohrt oder kunstvoll gegossen werden.
Zehn von 310.000 Ersatzteilen drucktauglich
Der 61-jährige Peter Sander leitet bei Airbus in Bremen die Abteilung „Material- und Prozessentwicklung“. Sein zehnköpfiges Kernteam ist europaweit vernetzt mit etwa 100 Kollegen, die seit 15 Jahren an dieser Revolution für den Maschinenbau und die Logistik arbeiten.
Derzeit sind zehn der 310.000 Ersatzteile der Airbus-Passagierflugzeuge im 3-D-Verfahren herstellbar. Ein großes Problem sei noch der Druck mit mehreren Materialien, auch ließen sich viele Metalle nicht verschweißen, so Sander: „Wir setzen im Flugzeugbau 30 verschiedene Aluminiumlegierungen ein, nur zehn sind drucktauglich.“ Gut geeignet seien Kunststoffe, die auch mit herkömmlichen 3-D-Geräten auf dem Airbusgelände im Heißklebepistolenprinzip verarbeitet werden. Kleinteile seien so als Prototypen entstanden.
Metallteile aus Varrel
Metallteile lässt das Werk hingegen in Varel herstellen – in den Werkhallen der 100-prozentigen Airbus-Tochter Premium Aerotec. Zehn 3-D-Drucker stünden dort, so Sander. „Die kleinen kosten 250.000 Euro, die großen schon zwei Millionen Euro, können aber auch ganze Automotorblocks fertigen.“ Eine Kooperation mit Mercedes laufe.
Im Jahr 2014 wurde die Metallteile-Produktion aufgenommen, mit einer Halterung für Küchen- und Wandelemente der Flugzeuge. Zwölf Zentimeter lang ist das erste Objekt. „Als Werkstoff haben wir Titan zum Verschweißen gemahlen, das ist hochfest und leicht“, sagt Sander. „Je leichter unsere Bauteile, desto leichter das Flugzeug, desto weniger Kerosin braucht es.“
120 bar Druck
Richtig in Serie gehen könnte 2020 eine 15 mal 12 mal 8 Zentimeter große Hydraulikeinheit (Foto), mit der das Aufstellen der Bremsklappen an den Flügeln gesteuert wird. Auszuhalten ist dabei ein Druck von 120 bar. „Seit 2010 haben wir daran gearbeitet“, so Sander.
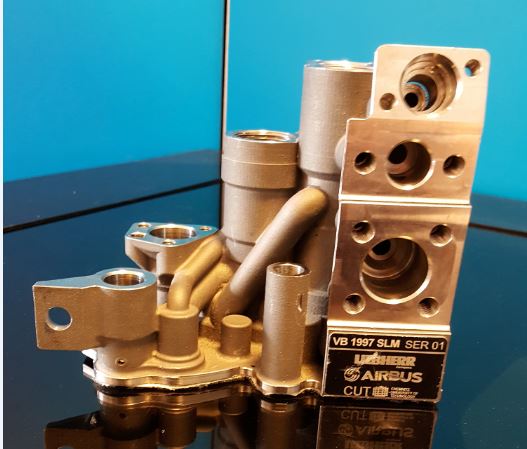
Frisch aus dem 3-D-Drucker: Hydraulikblock für die Landeklappe des A-380.
Jetzt sind die Computerzeichnungen des hochkomplexen Teils in Parameter für die Druckmaschinen übersetzt, so dass diese wissen, mit welcher Geschwindigkeit und Stromstärke der Laser welchen Weg durch das Titanpulver nehmen und dabei Schicht für Schicht fertigen soll.
Kein Verschnitt oder Abfall
Da jede nur sechs Hundertstel Millimeter dick ist, wundert es nicht, dass der Druckprozess 48 Stunden dauert. Einen Zeitgewinn ermöglicht das neue Verfahren also derzeit nicht, die geringe Geschwindigkeit verhindert bisher auch den Einsatz für die industrielle Massenproduktion.
Sander: „Da wir mit Titan arbeiten, ist unsere Hydraulikeinheit aber 55 Prozent leichter als in der herkömmlichen Fertigung und wir haben 75 Prozent Materialersparnis, so dass die Produktion zehn Prozent günstiger ist als zuvor.“ Es gebe halt keinen Verschnitt oder Abfall wie beim Herausmodellieren aus einem Metallblock.
„Seerose entwickelt – und gedruckt.“
Bremen sei ein „3-D-Druck-Hotspot“, so die Wirtschaftsförderungsgesellschaft. Die Airbus-Tüftler stehen mit einem vier Meter langen Flieger sogar im Guinness-Buch der Rekorde 2018, da sie als erste ein komplettes Flugzeug gedruckt haben, das tatsächlich in die Lüfte entschweben kann. Sander schwärmt von der Zusammenarbeit mit Firmen der Werkstoff- und Verfahrenstechnik im Technologiezentrum.
Im Bereich Bionik kooperiert Airbus mit der Universität: „Die Evolution hatte Jahrmillionen Zeit, mit minimalem Einsatz von Ressourcen maximale Effekte zu erzielen“, erklärt Sander, „wir schauen uns nun Lösungen der Natur an und übertragen sie auf unsere Bauteile, um noch mehr Material zu sparen. Gerade haben wir ein Wandelement für unsere Flugzeuge nach dem Vorbild einer Seerose entwickelt – und gedruckt.“